
ANSI/ISEA 105-2024: What You Need to Know
Safety Training
See All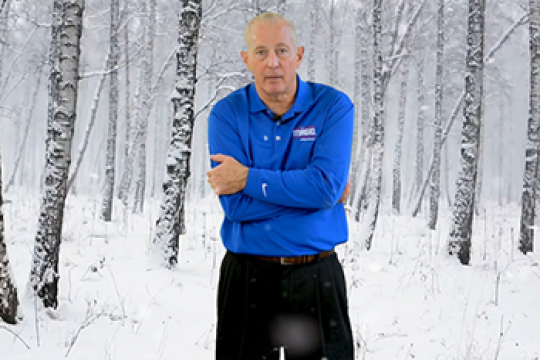
How to Treat Hypothermia on the Job
Anyone working in the cold is at risk for hypothermia. And while we usually think of it as an outdoor problem for agriculture or construction workers, even indoor workers in freezers and other cold environments can be susceptible.

What is Hypothermia?
Hypothermia happens when your body loses heat faster than it can produce heat, causing a dangerously low body temperature.

What Causes Hypothermia?
Hypothermia can be caused by exposure to cold conditions or immersion in cold water. When your body temperature drops, your heart, nervous system, and other organs can't function normally. Left untreated, hypothermia can lead to complete failure of your heart and respiratory system and eventually to death.

Hypothermia Symptoms
Shivering
Slurred Speech or Mumbling
Slow, Shallow Breathing
Weak Pulse
Clumsiness or Lack of Coordination
Confusion or Memory Loss
Drowsiness or Very Low Energy
Loss of Consciousness
Hypothermia Treatment
- Call 911 or get medical help immediately if you suspect hypothermia.
- Handle your worker with care. Excessive or vigorous movements can trigger cardiac arrest!
- Move your worker out of the cold if possible. If not possible, shield your worker from the cold and wind.
- Remove any wet clothing. If necessary, cut clothing away to avoid any jarring movements.
- Cover the worker with blankets. Cover their head and leave only the face exposed.
- If youāre outside, lay your worker on his or her back on a blanket. Donāt lay them directly on the ground.
- Monitor breathing. A person with severe hypothermia may fall unconscious. If the person stops breathing, begin CPR if youāre trained.
- If the person is alert, give them a warm beverage.
- Apply a first-aid warm compress on the back of the neck, chest, or groin. Don't apply a warm compress to the arms or legs. Heat applied to the arms and legs forces cold blood back toward the heart, lungs, and brain, causing the core body temperature to drop even more. This can be fatal.
Cover Up
Make sure your workers cover their head, neck, and face when working in cold conditions.
Don't Overexert
Avoid activities that cause workers to sweat too much. Wet clothing and cold weather cause body temperatures to drop quickly.
Dress in Layers
Have workers wear layers to trap heat near their body. Wool, silk, or polypropylene inner layers hold body heat better than cotton does.
Stay Dry
Make sure your workersā cold weather gear is water repellent. If they do happen to get wet, have them get out of wet clothing as soon as possible. Make especially sure workers keep their hands and feet dry while on the job.
Send your workers a quick safety training video to remind them how to prevent hypothermia! GIVE ME VIDEOS |
Download our FREE Cold Weather Safety Training Presentation to teach your workers how to stay safe in cold weather conditions! SHOW ME TRAINING |

Respirator Mask Training: 3 Safety Tips

7 Tips for a Better Workplace Ergonomics Program
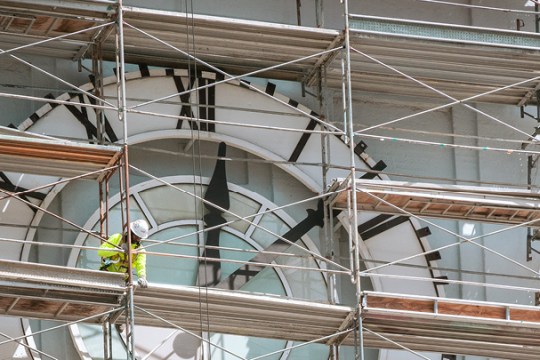
How to Train Workers for Scaffolding Safety
Safety Culture
See All
6 Ways to Deal with Opioid Use Disorder in the Workplace

Safety Tips: The Power of Employee Empowerment
Employee empowerment is something we usually see discussed in the pages of Forbes or Businessweek, but empowerment is just as important for you and your workers as it is for the C-Suite. In fact, given that safety is on the line, it may be even more important.
Weāve spoken to safety managers in various industries about how they empower their workers. Their tips break down into three concepts - encourage workers to speak up, give workers a mission, and let workers make decisions.
Encourage Workers to Speak Up
One of the easiest ways to empower someone is to give them a voice. You can find new and unique ways to empower workers from asking them to speak in meetings to recognizing and rewarding their efforts.
Have Smaller Safety Meetings
Break your safety meetings down into groups of no more than five or ten people. Smaller groups often make people more comfortable and encourage them to speak up if they have concerns or ideas.
Let Workers Help Choose PPE
Have all of your workers test samples of new PPE under consideration. This kind of worker input can have a significant impact on compliance.
Offer Rewards for Speaking Up
Try an incentive program to encourage workers to report existing or potential hazards as soon as they see them. The more safety hazards a worker reports, the more rewards they earn.
Give Workers a Mission
You can also empower workers by giving them a mission to accomplish.
Assign a Point Person
Choose a worker to be in charge of each area or function. Make them responsible for the safety of their areas and for telling their supervisor about any risks or challenges. It gets more people engaged and helps to build a safety culture.
Assign New Workers a Mentor
Assign freshly trained workers a mentor who is responsible for showing them how to apply the training they just completed and guiding them through their first project. New workers get the advice they need and the mentor knows you trust and value them.
Spread the Safety Enthusiasm
Find a worker with a positive attitude and make them an ambassador for safety. Have them show and tell others about the benefits of proper PPE and get people enthusiastic. It inspires people to work more safely in a fun and friendly way and empowers the āPPE Ambassadorā to help make changes in the workplace.
Let Workers Make Decisions
Thereās nothing as empowering as being able to decide your own fate. Give workers the power to decide some things for themselves.
Link Safety to Promotions
Require workers to demonstrate that they have done something to improve safety outside of their immediate work area before theyāre considered for a promotion. This makes safety an essential route to success and gets your safety-minded workers into positions of leadership.
Take Time Out for Safety
Take empowerment down to an individual level. Let workers know that theyāre free to take a break at any time to invest five minutes to check that safety protocols are being followed. While some companies expect workers to keep their nose to the grindstone, sometimes the safest policy is to encourage people to step back and take a moment to think for themselves.
Give Workers PPE Ownership
Whenever possible, offer two or three products that meet the safety needs for each job. Then let each worker pick which item they like best. If they arenāt wearing the right protection, you can ask, āWhy arenāt you wearing that glove you picked out!?ā It gives the worker a feeling of ownership and makes them more likely to comply since it wasnāt forced on them.
Expecting workers to just follow the rules can not only feel stifling for them, it can cause you to miss out on new ideas and observations that you can only get from workers doing the job. Try some of these ideas and see what a difference a little empowerment can make!

Looking for more ideas? Check out this webinar on ways
you can keep workers safer while making your job easier!
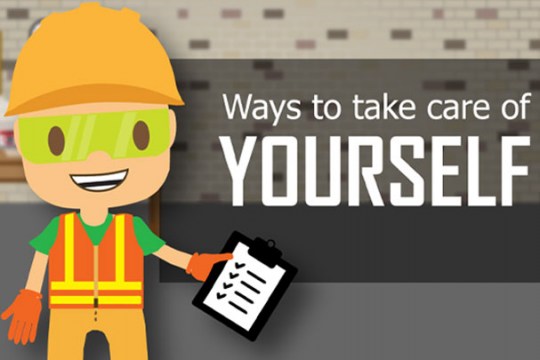
6 Ways to Reduce Work Stress for Safety Managers
Itās hard to build a safety culture when youāre tearing your hair out. Being responsible for the safety of your employees is a huge job in the best of times. Add in world events, supply chain issues, and changing laws and regulations, and your stress level may be off the charts. Meanwhile, cuts and lacerations, arc-flash, slips, trips, and falls, and all the hazards you normally deal with are still part of the job. So how can you keep your sanity with all you have to do? Try these six tips!

Stress Relievers to Make Your Job Easier
1. Plan Time to Plan
No matter what else is going on in the world, your companyās leaders expect production as usual and your customers are still looking to get their orders filled. That doesnāt mean you have to start putting out fires the moment you arrive for the day. Take ten minutes first thing in the morning to clear your head and organize and plan your schedule for the day or even for the week. Use digital calendars and planner apps to keep you organized and block out time when you need it. Thereās nothing wrong with a planning meeting you schedule with yourself!
2. Reassess Your Routines and Schedules
Time is the biggest constraint for most safety managers. Carve out some time to audit your work schedules and daily routines to find inefficiencies. Although reworking larger operations can be a massive investment of time and energy, making smaller changes can be a fast and easy way to cut out redundant tasks and find opportunities to delegate.
3. Delegate Tasks to Your Employees
You canāt do it all yourself. Delegating tasks to some of your best employees will free up your time and give you more breathing room in your busy schedule. Your safety committee is a good place to find enthusiastic employees who want to make your workplace safer and perhaps even move up the ladder to take on more responsibility. Find your safety leaders and leverage them to reduce your own stress!

Stress Relievers for Safety Professional Wellness
4. Monitor your Stressors
Never forget that youāre just as human as your employees! Chronic stress can lead to symptoms like anxiety and high blood pressure as well as unhealthy coping habits like overeating. If you recognize situations that cause stress symptoms like headaches, stomachaches, anger, or frustration, take a moment to consciously note what set that stress in motion. Over time, you may be able to recognize these stressors when they occur so you can figure out how to change whatās causing them. For example, if you find yourself stressing every time you need to remind employees to wear their safety glasses, you can think about implementing new mentoring or training programs or even posting more safety reminders to take some of the pressure off of you.
5. Give Yourself a Break
When you feel the stress building, take a moment to step back and re-center your focus. Get up and stretch or walk around to get your blood flowing and switch your focus for a short while. Even closing your eyes and concentrating on your breathing for a few moments can slow your heartbeat and stabilize your blood pressure to help you think more clearly when you return to the task at hand.
6. Establish Boundaries
Establish boundaries to start or end your day on a controlled, focused note. Listen to music, your favorite sports radio, or a book on tape during your commute instead of thinking about work. After work, avoid checking your phone during dinner or family time so you can maintain a firm barrier between your work life and your home life, when possible.
Save yourself some time with our FREE,
ready-to-download safety training resources!
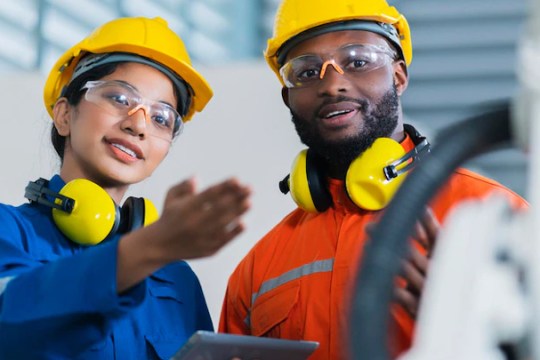
Safety Tips from Safety Managers
PPE: Choosing & Using
See All
3 Steps to Saving Money on PPE Cost
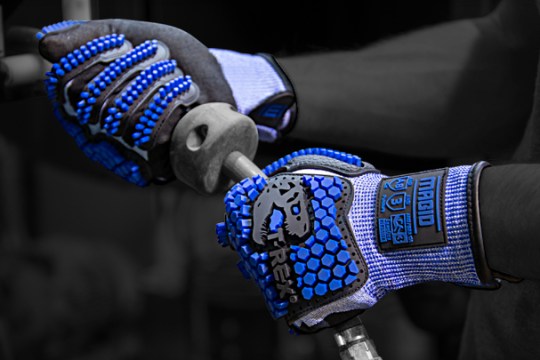
An Evolution in ANSI Level 3 Impact Gloves

PPE: How to Get Your Moneyās Worth

21-Gauge Cut Resistance Just Got Even Better
Safety Managers' Secrets
See All
Give a Safety Pop Quiz
Shared By Ralph, Safety Manager, Manufacturing & IT
I like to give my workers random safety pop quizzes for a prize. For example, Iāll ask if anyone can recite at least five of our ten safety protocols. If they can, they get a t-shirt.
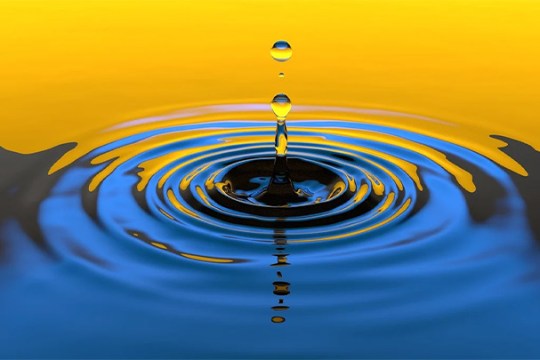
Emphasize The Ripple Effect
Shared By Ed, Safety Manager, Oil & Gas
When talking about safety, I make sure my people know, if you get injured, itās not just you that suffers, itās 120 families. An injury means an OSHA recordable. That means our OSHA Incident Rate goes up and that might mean we canāt have our company picnic or I canāt give promotions. So when you think about picking up that heavy box by yourself, think of everyone else!
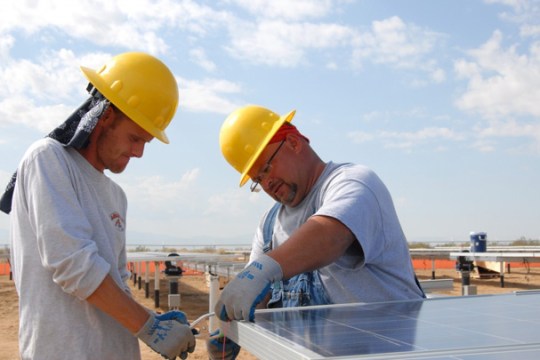
Assign New Workers A Mentor
Shared By Kevin, Safety Manager, Oil & Gas
We put our new hires through workshops, lectures, online training courses, and other traditional forms of training, but once they complete that, they are assigned a mentor from our safety team. The mentor is responsible for showing them how to apply the training that they just completed and guide them through their first project. By implementing this program weāve eliminated 1.5 to 2 million dollars a year in unnecessary wait time for redoing work.
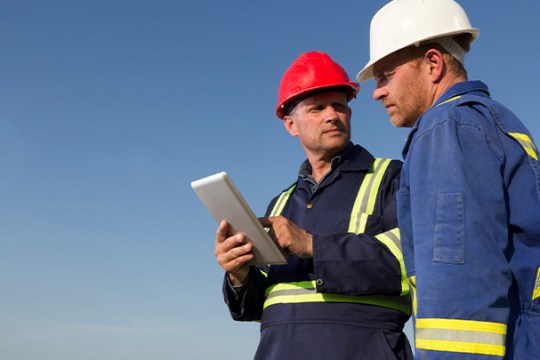
A Little Teasing Can Save a Worker's Hearing
Shared By Sean, Safety Manager, Manufacturing & IT
When I see people not wearing their hearing protection, I walk up to them and start ātalkingā but I donāt make any sound. Itās a friendly reminder of what they might experience if they damage their ears!